Warehouse racking – How do you organise a warehouse efficiently?
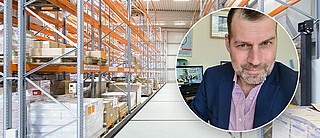
Getting your warehouse racking right and working around your operational needs can bring huge time and cost saving benefits. But how do you organise a warehouse efficiently? In this interview, we ask Advanced Applications, Racking Specialist Brad Kilian, how racking systems can improve efficiency and what the current trends are when it comes to racking solutions.
What is a warehouse racking system and why is it so integral?
In the simplest term, a racking system lifts materials and goods off the warehouse floor and utilises the vertical space available in the building. The most efficient solution for any warehouse is for there to be no storage at all; goods come in, are processed and are then forwarded on to the end user. However, warehousing is a necessary requirement and one that STILL, makes every effort to make a cost effective, streamlined, process driven environment. One where goods and materials flow through, with as few handling opportunities as possible and a racking system to try and manage the flow through, taking into consideration, seasonality; bulk storage requirements, supply and demand and in this day and age; a global pandemic.
Without an effective racking system you will eventually discover, lack of control over the material that comes in and where it is stored (a good WMS is essential to obtain a good outcome as well); resulting in goods being hard to access and slowing down the handling operation. With an optimised racking system for the goods which your warehouse handles, the space available and the material handling equipment present, you have a real opportunity to drive efficiencies in your warehouse. At the end of the day, warehouse managers want to save handling time, improve safety and reduce product losses, and that's exactly what a well-designed warehouse racking solution can achieve.
How can racking improve warehouse efficiency?
Primarily a well-designed racking system will cut down on handling time in your warehouse, decrease the need for multiple handling of the same pallet. The second phase is to make use of different racking systems (Standard Adjustable pallet Racking, Live Racking, Push Back or drive in) and this is tailored not only to the material you are handling, but also the Materials Handling Equipment being used.
With warehouse racking systems, we always say ‘one size does not fit all’; for a start there are so many different variables to consider such as warehouse space, supply chain, available material handling equipment and the goods themselves. Our role in Advanced Applications is to create a system designed to move material and goods through a warehouse as efficiently as possible. In some scenarios we may have two very similar companies handling very similar goods, however due to any one variable, the ideal racking solution will be entirely different.
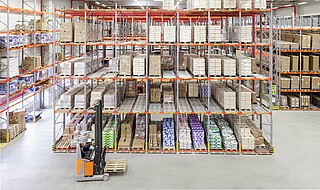
What are the different types of racking systems available from STILL and how do they fit into STILL's overall service offering?
At STILL, we offer every kind of racking system from a light picking solution to a very narrow aisle high bay racking system and every type in between. We offer Drive In racking, Mobile Pallet Racking, Shuttle Systems, cantilever systems and Mezzanine floors, all designed specifically around the clients’ available space and warehousing needs. The reason we supply so many types of racking goes back to the ‘one size does not fit all’ approach and hence we offer free consultation within the Advanced Applications team at STILL.
We create solutions that are optimised for the client and in my view, this is the most important aspect of what we do at STILL. Where a dedicated racking only supplier might design a system that maximises warehouse space, we consider the flow of goods through that space, and how the trucks and pickers are able to handle the goods. Our approach ensures that the warehouse environment actually works for the customer.
Would every business benefit from a custom racking solution?
Almost certainly, every business would benefit, as their needs differ so much. Our consultation process starts with understanding what the client is looking to achieve from their warehouse, we ask questions to understand what product lines they handle and the equipment they use to handle it. From this we could recommend a racking solution that suits, maybe it’s a wide aisle application as the client will be using the counterbalance for indoor and outdoor process with restricted roof heights, maybe they are using a Reach truck which allows us to narrow down the aisle somewhat and achieve a higher top beam - the options are endless and we take pride in being able to offer both advice and solutions (handling equipment included), that meet the need of every individual client.
We will find even small differences in stock movement or employee shift patterns which can influence the design of our solution, especially the racking systems used. For example, the racking system used on the same product handled in two similar warehouses could end up being a bulk store system in one (Drive-in racking FIFO / LIFO system) and a shuttle system in another.
Our complete solution approach is where I think we really add value to the customer; we can utilise the whole STILL product portfolio of racking systems, materials handling equipment and management software to create the ideal design. This results in a harmonious warehouse solution and a ‘one stop shop solution’ for the client.
How do Push-back and Shuttle Racking systems work?
Push-back Racking and Shuttle Racking systems work on the principle of trying to achieve product storage density, so being able to store pallets as close together as possible. By removing space between the frames and pallets, you can increase the density of your goods stored. A Push-back Racking system relies on a forklift or reach truck to push the goods into position to create the storage density required, making use of either channels or rollers, to aid the movement of the load.
Shuttle Racking systems take that principle a step further by adding in automation. Here, instead of using a truck, the Shuttle Racking system handles the movement at a push of a button, placing the goods into a dense footprint with a lot less movement by your material handling equipment.
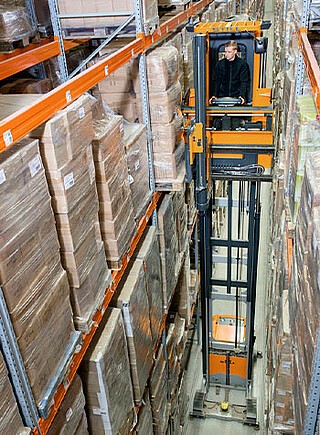
Are Shuttle Racking systems safer?
Absolutely, with a Shuttle Racking system there's less movement in the actual channels from your material handling equipment, and as a result, less risk of accidents and damages. It’s not just safety you are benefiting from either, there are cost benefits too. With a Shuttle Racking system there is less wear and tear on the racking frames (less damages) and less usage on your trucks. A shuttle system handles your goods in a controlled automated environment, so pallets aren’t pushing against each other (or loads for that matter), all these allowances are made by the use of lasers, to ensure no product damage.
What trends in warehouse racking are you seeing?
Over the past year we have really found clients asking for automated processes in their warehouses, and solutions – our Pallet Shuttle system can offer this. While it may not suit clients that handle a wide variety of goods, you could still automate a specific chain or product line in your warehouse with a shuttle system.
Another big trend we're finding with clients is space utilisation and bulk storage. Since coronavirus, there's been a tremendous upturn in online shopping. To supply this demand, clients are looking to utilise every square meter of warehouse space with high-bay racking systems (if their product lines require this), enabling them to pick and store goods at higher levels using our fantastic VNA trucks. Mezzanine and multi-level systems have also grown in popularity too, creating more floor space in the same footprint. A lot of warehouses have seen an uplift in small order picking as they adapt to online shopping habits and fast delivery demands and by combining racking, low level order pickers and even EK and MX trucks to pick from height, we have been able to meet and exceed the demands of this fast moving industry.
Is it time for an intralogistics consultation?
At STILL, we act as a partner to develop a ‘one stop shop’ solution for your warehouse that can bring both efficiency and cost savings. Whether it’s an automated space saving Shuttle Racking system or adapting an existing warehouse to manage increased demand. Our experts in Advanced Applications are on hand to offer their support. Contact us to find out more.
Comments
No comments
Subscribe to the blog !
Be informed as soon as an article is published. You can unsubscribe anytime.
Leave a comment