8 tips to drive down costs when optimising your warehouse fleet
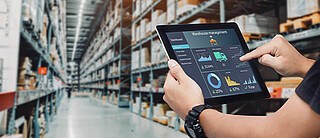
If you asked most businesses why they decided to optimise their warehouse fleet, the chances are that cost would be a big driving factor. Upgrading equipment and implementing new management systems is often cost-effective in the long run but there are still plenty of considerations to be made when deciding on the best solution. The logistics industry is under increasing pressure thanks in part to the rise of eCommerce, home shopping and customer expectation when it comes to quick deliveries. With growth comes rising costs, and the bigger the growth the bigger the costs of logistics. A prime example of this would be Amazon who saw huge increases in revenue in 2020, and also saw a 61% increase in year-on-year shipping costs to a whopping $61.1 billion, which highlights the need to balance operating costs and maximise profits.
In this blog, we look at 8 top tips for driving down costs when optimising your warehouse fleet.
1. Review your vehicle fleet
Is your warehouse fleet up to date? If you’re looking to drive down costs in the long-term this is a good place to start. Advances in technology and innovation mean that modern day vehicles are fitted with powerful features to help maximise fuel efficiency and allow safe and efficient operation. When optimising your warehouse fleet, it’s always worth reviewing your current vehicles against what’s currently on the market and deciding where investing in more modern vehicles can drive down your operating costs and improve productivity. Always check to see if a universal specification can complete more than one task and allow for fleet utilisation to be maximised.
2. Make time for maintenance
Of course, getting the right vehicles in your fleet is important but an efficient maintenance schedule is essential. Fleet downtime is never ideal but when effectively planned costs and disruption can be kept to a minimum. Unexpected downtime is often harder to manage and sees higher costs for more significant repairs. As well as scheduling maintenance and health-checks, you can also invest in diagnostics software to keep an eye your vehicles and identify potential issues before they become a problem. Fault codes and alerts detected early on can mean fixing a small issue before it turns into a costly repair following a breakdown. That’s where fleet management software comes in.
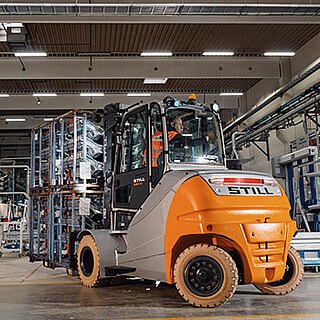
3. Implement a fleet management system
Having a fleet of warehouse vehicles operating is one thing. Having them operating efficiently is another. That’s where a fleet management system like STILL’s neXXt fleet comes in. A comprehensive management system can keep track of an abundance of vehicle data and condense it into a dashboard to give you an overview of your fleet and its performance at any time. As well as having basic vehicle overviews at a glance; you can keep track of financial information and maintenance costs, as well as comparing data from different locations. Are vehicles in one warehouse operating far more efficiently than the same vehicles in another warehouse? By monitoring how your fleet is performing, you can identify any behaviours or tasks which are driving up costs, like excessive fuel consumption or potentially hazardous activity. This is also a credible way of establishing real-time usage of equipment vs historic hearsay when it comes to the fleet mix.
4. Train your operator team
Loss and damage in the warehousing process is one of the biggest cost drains for businesses. It’s estimated that 1% of product stock in warehouses is damaged every year (source; Warehouse Logistics International). It may not sound like much, but it equates to $50 billion lost globally every year, and that figure doesn’t include the cost of any damage done to vehicles or the warehouse itself. From damaged goods to damaged infrastructure, the cost of replacements and repairs to equipment and products can quickly mount up. Having an efficient, cost-effective warehouse fleet isn’t just about having the best vehicles, it’s about having the right people to operate them. That’s where investing in your staff training can pay dividends. Not only can you keep your operators safe in the workplace with the right training, but you can minimise costs associated with accidental damage to the stock and warehouse caused by improper use of vehicles by ensuring the team operating them are doing so correctly and efficiently. The true cost of down-time and that potential lost client can never be truly understood or regained.
5. Increase efficiency levels with semi automation
One way of driving down your operating costs is to increase the efficiency and productivity of your vehicle operators. Semi-automated warehouse trucks and forklifts can hugely benefit a business drive down operating costs through a reduction of lost time and worker inefficiency. Automated vehicles and order pickers come with a range of features to keep workers safe and comfortable and allow them to do their jobs more easily. Overall labour costs often make up the around 65% of warehouse operating costs so keeping staff safe and making their jobs easier can contribute hugely to driving down costs. Compared to manually operated order picker trucks, a semi-automated version can increase operator efficiency by up to 20%, saving both time and money in warehouse operations which in turn also means operators finish their shift fresher and fitter than ever before.
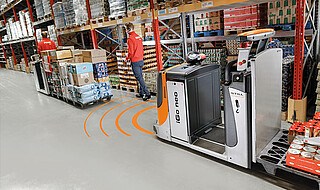
6. Talk to the experts
No matter what your ultimate goal is for optimising your warehouse fleet, driving down costs will always be an important factor and will perhaps be your primary aim. That’s where working with an expert consultancy firm can be beneficial. They can assess your operations and optimisation goals and propose cost-effective solutions and recommendations, as well as seeing them through to implementation. While some businesses may be hesitant to pay consultancy fees, the cost-savings in the long term can easily outweigh that, and experienced consultants like STILL can help you optimise your fleet to maximise cost-efficiency. Experts can independently assess your existing or proposed fleet and draw up utilisation concepts to ensure optimum capacity utilisation and efficiency to make sure you are getting the best and most cost-effective use out of your fleet, whilst at all times keeping the solutions simple and manageable.
7. Utilise a warehouse management system
With the demands on warehouse logistics always increasing, management systems are proving to be essential in running them. Whether your goods are delivered B2B or B2C, there is ever-increasing demand for lower shipping costs, faster deliveries and effortless returns. Gone are the days of clipboards and checklists. Today’s warehouses can run far more efficiently with a warehouse management system (WMS) which allows teams to control stock, deliveries, order picking and dispatch from a central location. A good WMS lets you control every movement of goods within a warehouse from a central, from goods received and stock control to order picking and distribution.
8. Fuel efficiency and a green future
One of the trends we’ve seen in 2021 has been the continued growth in sales of electric forklift trucks as many businesses move toward greener and more cost-effective vehicles. We previously mentioned the efficiencies that can be gained from modern vehicles, but the benefits of electric vehicles go beyond fuel-efficiency. Investing in an electric fleet is not only an effective way to drive down costs in the immediate future but, with a complete ban on combustion-engine vehicles planned for 2030, it’s likely electric is the future for the country. Other benefits of removing any combustion engine (and their related exhaust waste product) from the warehouse environment include noise pollution reduction, saturated gases that lead to nausea elimination and remove carbon build up on the goods in storage. Electric vehicles also have the advantage of a smaller footprint for the same carrying capacity. This can release space and reduce both truck and product damage.
In addition to that, red diesel, commonly used in commercial, off-road vehicles, will only be available to select industries from April 2022. Operators in industries like commercial warehouses and logistics operations will no longer be able to buy and use red diesel from April. Instead, effected businesses will need to switch to regular “white” diesel which has a duty rate of 57.95 pence per litre (as of March 2021). This duty change will have a huge financial impact on businesses that currently use red diesel for their warehouse fleet and will be an essential consideration for any business looking to drive down operating costs for the future.
Find out how our professional team can help
We can help your business improve warehouse efficiency, if you need advice on any of the topics or products mentioned above, please feel free to Contact us today!
Comments
No comments
Subscribe to the blog !
Be informed as soon as an article is published. You can unsubscribe anytime.
Leave a comment