How automated guided vehicles and forklifts (AGVs) are shaping safe and efficient warehouses
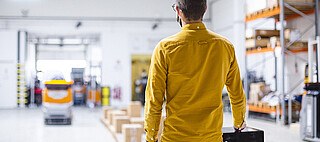
Industry 4.0 has bought about huge changes in how warehouses operate, and automation is becoming a big part of this new industrial revolution. The developments in technology and robotics have led to an increase in the number of automated systems being integrated into modern day warehouses. According to a recent government report on The Economic Impact of RAS Across UK Sectors, estimates of current robot density (robots per million hours worked) highlighted significantly stronger uptake in the warehouse logistics and food & drink manufacturing sector than other industries.
The current range of Robotic and Autonomous Systems technologies, which include logistics applications such as automated guided vehicles, mobile retail robots and autonomous mobile robots (AMRs), have been a huge benefit to the logistics industry. AGVs are material handing vehicles which are designed to work autonomously, and automated guided forklifts in particular are proving popular in warehouses.
However, it’s not always feasible or even desirable to separate autonomous machines from human workers and that’s where automated guided forklifts are proving their worth. These specialist trucks are designed to work alongside human operators, utilising the power and consistency of a machine to enhance human efficiency and minimise the risk of overexertion or injury.
So, how are automated guided forklifts bringing these benefits to warehouses?
How do automated guided vehicles work?
AGVs are driverless vehicles which are designed to follow a pre-programmed path or follow operators using a location tracker on their person. Advances in technology over the last decade have allowed AGVs to be programmable without the now-outdated need for lines with wires to follow. They use sophisticated sensors to avoid collisions with other vehicles, warehouse infrastructure and other workers operating in the area. Automated guided forklifts in particular are designed to help operators by taking the strain of repetitive and/or high-stress tasks such as lifting and reaching. Their consistency and reliability all but guarantee efficient operating and the myriad safety features can help limit accidents caused by human error and injury to operators themselves.
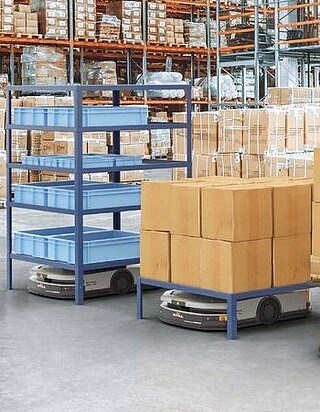
What are the applications of automated guided forklifts?
Automated guided forklifts have huge potential and can be used on a variety of sites depending on the needs of the business. These include;
Navigating tight spaces
Systems like STILL’s iGo pilot Navigation can be linked to specific warehouse topography, stopping forks at exactly the right height and avoiding contact with the racking thanks to pre-programming and sophisticated sensors.
Order picking
Order picking is becoming increasingly common in warehouse logistics thanks to the rise in home delivery. Fulfilling orders from a vast warehouse can be inefficient and time-consuming for human operators alone, but AGVs can help. Like the STILL OPX-iGo neo, autonomous order pickers follow the operator, stopping at the optimum picking position to increase operator efficiency.
Point-to-point transfer
One of the key benefits of AGVs is the ability to automate repetitive tasks – particularly when those involve the transfer of heavy or potentially hazardous loads. Point-to-point transfer can be a simple task for AGVs, removing the requirement for human operators to manually transfer loads back and forth.
Picking up and putting away
Quickly moving deliveries out of a loading dock is essential in a busy warehouse and this can be a time-consuming manual task. The time required to facilitate the transfer and storage of goods becomes even longer if the warehouse uses high racking. AGVs can be easily programmed to transport bulk items to racking and/or offloading to different vehicles for storage. This integration of horizontal and vertical automation brings together smaller, more agile AMRs with high-reaching AGVs. At STILL, we’ve likened this to David and Goliath working together to maximise warehouse efficiency.
Hazardous material handling
Automation is often used to supplement human labour but there are times when it’s safer and more efficient to remove humans from the equation all together. Transporting hazardous loads is an ideal time to do just that, and automated guided forklifts can be utilised to prevent as many people as possible from coming into contact with hazardous loads and substances.
The benefits of utilising automated guided forklifts in warehouses
Warehouses are faced with ever-increasing challenges when competing for satisfied customers. The demand is for faster fulfilment, more complex requirements and better value. Automating your logistics process – or even just part of it – can reap huge rewards in terms of efficiency and worker productivity.
Endurance without fatigue
It’s estimated that fatigue costs the UK £115-£240 million per year just in terms of workplace accidents. In today’s modern warehouse, where operations can run 24/7, a decrease in worker efficiency over an eight-hour shift is somewhat expected. AGVs are designed to “lighten the load” on their operators and assist their performance. For example, the STILL OPX-iGo Neo predicts a 75% reduction in instances of strenuous mounting and dismounting, as well as a considerable reduction in walking distance.
Reduced cost of errors
Automated systems are, by and large, far less fallible than human workers. A report from global analyst firm IDC discovered that the estimated cost to US and UK businesses from employee error was £18.7 billion (Counting the cost of employee misunderstanding - IDC, Framingham, MA, US, 2008). Damaged stock, shipping errors and vehicle down time can be costly. Whether it’s workplace accidents, mistakes leading to delays or inefficient operator processes, there are many ways a warehouse can lose money unnecessarily. AGVs help reduce, and potentially eliminate, these costs thanks to consistent and reliable operating.
Safety for workers
The improved safety that can come from utilising AGVs is twofold. First, these vehicles are designed to take the strain off human operators by automating repetitive or dangerous tasks. Second, a wide variety of safety features and sensors means the risk of impact is minimal. Unlike manually operated vehicles, which can strike pedestrians or trucks if the operator isn’t paying attention, automated vehicles will stop themselves before a collision can occur, whether this is other workers, trucks or warehouse infrastructure like racking or stock.
Maintain warehouse capacity
Hiring and retaining staff has long been an issue and it’s one that isn’t going away. In fact, the shortage of warehouse workers in the UK has caused a 30% spike in wages (Reuters, 2021) as companies fight to keep staff. Labour shortages can threaten a warehouse’s ability to cope with demands, especially at peak times. The use of AGVs can help to mitigate some of these issues by reducing the need for operator intervention, as well as increasing the overall efficiency of the warehouse and freeing up staff to work on other tasks.
For the automation of forklift trucks, STILL offers a uniquely comprehensive range of standardised and scalable solutions. This means that automation projects can be implemented easily at any time. In this way, any company, regardless of its size, can reap the benefits of automated transport processes. Contact our team to find out more.
Manufacturer recommendations and hours of use
A common question when it comes to forklift truck servicing is; how often does a forklift truck need to be serviced? Unfortunately, there is no straightforward answer to this question because servicing requirements vary between types of truck, truck manufacturer and degree of use. Manufacturer guidelines will recommend servicing intervals dictated by the age of the forklift or hours of use (whichever occurs first) and it’s important to make sure that your servicing schedule accounts for this. Failing to adhere to these recommendations might seem like a way to reduce servicing costs, but it’s likely to cost additional time and money in the long term. There are also a number of legal obligations and industry guidelines that require warehouse equipment – especially trucks and lifting equipment – that must be adhered to.
Comments
No comments
Subscribe to our blog!
As soon as a new article is published, we will notify you! You can unsubscribe at anytime.
Leave a comment