What does MHE fleet management software do? The cost benefits
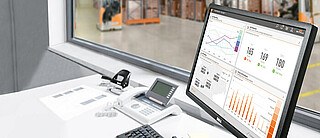
Fleet management has become increasingly important in the rapidly-growing logistics industry. Having the right range of vehicles operating in a warehouse is one thing, but the right fleet management software is key to keeping them running efficiently. In this blog post, Amy Tomlinson, Project Coordinator at STILL, discusses the cost benefits of fleet management software.
What is fleet management software?
Fleet management software is a web application that uses real-time data to provide full transparency of a vehicle fleet and how it is operating. The fundamental goal of the software is to help customers attain cost savings and manage their fleet operations. It focuses on the utilisation of the fleet, identifying patterns and areas for improvement, which can provide significant cost savings in the long run. Fleet management software takes a huge amount of data about your vehicles and displays it in one place so it can be easily reviewed and acted upon if necessary.
What fleet management products does STILL offer?
Not only do we offer our customers a long-term fleet management consultancy service, we also offer two main products so customers can manage their own fleet both operationally and financially.
FleetManager™ 4.x manages access authorisation and shock detection, plus it provides an extensive suite of reporting functionalities. It can also help increase worker safety by identifying impacts and the situations they occurred in, allowing the optimisation of fleets through the assignment of vehicles to operators, as well as reducing physical damage to trucks, goods and warehouses.
Then there’s STILL neXXt fleet, which is an innovative and powerful tool that bundles all relevant information for the user into a secure and easy-to-use web application. Commercial and technical data from SAP is combined with data directly from the trucks which is then displayed for analysis. neXXt fleet not only evaluates data but also automatically reminds users - optionally via system messages or emails - if cost levels are surpassed or key dates become due.
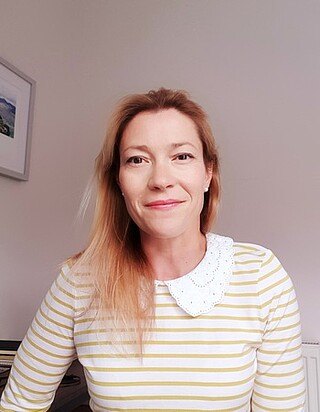
How does fleet management software offer cost savings to warehouse operations?
The software offers cost saving initiatives in several ways, depending on the specific software used. Generally, it gives operations managers an overview of the fleet so they can identify where cost savings can be made due to inefficient use or just to ensure that trucks are operating within set parameters. As an example, neXXt fleet allows customers to manage their spend by setting automatic alerts when vehicles are surpassing defined cost limits. FleetManager™4.x provides instant reports on truck utilisation over specified dates and areas that can help customers with shift patterns and maximising fleet usage, as well as highlighting areas where trucks are underutilised or could potentially be off-hired.
How does Industry 4.0 and increased connectivity benefit fleet management and enable cost savings?
Industry 4.0 is about revolutionising the way your entire business operates and grows. One of the key elements of Industry 4.0 is the introduction of smart technology which relies on ever-increasing amounts of data and interconnectivity between systems. It’s this data overview that lets users make cost-effective decisions and changes based on all the information.
By using ‘smart manufacturing’ we offer our customers a holistic approach to fleet management by providing them with the tools to manage all aspects of their fleet. Customers not only achieve cost savings from having full transparency, but also increased work safety too.
For example, FleetManager™ 4.x reduces physical damage by detecting unusual loads and can alert the operations team. In the event of unusual truck impact, a detailed report allows customers to introduce preventative measures. These are just a few of the ways we can help customers optimise their fleet and introduce cost saving initiatives by using real-time information.
Fleet management brings a lot of health and safety benefits to the warehouse? How does this benefit the operating costs?
FleetManager™ 4.x allows customers to define individual usage profiles for different drivers for each forklift truck. By managing the usage profiles, this ensures that only those permitted to drive certain trucks have the access to do so. The properties of the truck, such as maximum driving and lifting speeds, automatically adjust for each operator. The auto-logout function can be set as required, prohibiting the potential for another operator to drive the truck under someone else’s user profile.
When a truck registers an unusual impact, the driver, truck details and time are automatically sent to a selected group of recipients via an automated report. So, if someone is driving around the warehouse, going a little bit too fast and clips something, that will set off the shocks and a report will instantly be sent to the fleet manager who will have access to the incident information; truck details, driver details, the time of the collision, what speed the vehicles was doing, whether they were travelling backwards/forwards, if the operator seatbelt was fastened…lots of information that helps them identify incidents and patterns to avoid them happening again in the future. By having this information readily available, businesses can keep their operators safe and avoid repeat collisions that can cause costly damage to the truck, the goods and the warehouse itself.
Comments
No comments
Subscribe to our blog!
As soon as a new article is published, we will notify you! You can unsubscribe at anytime.
Leave a comment