Autonomous Order Pickers – the latest in warehouse efficiency
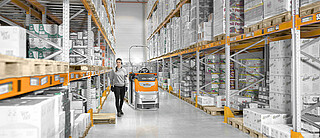
With the rapid rise of online shopping and the increasing pressures on suppliers to process, pack and ship orders as fast as possible, autonomous order pickers are becoming an increasingly vital part of company logistics. In this interview, Ray Ake, UK Systems Manager at STILL, talks about how autonomous order pickers are being integrated into warehouses and the benefits they can bring.
So, to start off, what exactly is an autonomous order picker?
An autonomous order picker is essentially a truck that follows the operator and automatically stops in the optimum picking position. They work in response to the operator and that particular person, and STILL are the first company to succeed in turning our series-produced trucks into autonomous assistants. Because the autonomous order picker follows the operator without the need for controls, it makes the unit much more efficient. The operator doesn’t have to climb on and off the machine or fiddle with controls, allowing them to complete their tasks more quickly and safely.
What is STILL’s iGo neo and how can it be integrated into an existingmanual handling system?
The iGo neo is our range of autonomous pickers that uses artificial intelligence to operate according to the user’s needs. They adjust mechanical power and speed to the task at hand and stop exactly in the optimum position. So, if the operator maybe wants to walk a bit faster, the truck will increase its speed slightly to keep up and remain in the perfect picking position. The iGo neo is part of the STILL OPX family and so comes with the same quality, values and standards as our regular trucks. The autonomous versions follow this design nicely, so for operators already familiar with manual pickers, they’re easy to use.
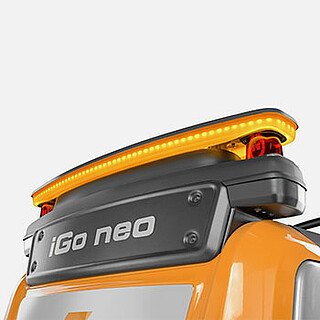
There are no structural changes required to integrate the autonomous order pickers either. If you’re already using order picking trucks, then the automated versions are an easy upgrade. And if you’re looking to introduce a more efficient order picker with automation from the start, the team at STILL can help you get started with the best solution.
What are the key technologies used by autonomous order pickers?
The technology used is all geared towards increasing productivity while ensuring safety. For example, we have what we call a hybrid tracking system that monitors 360 degrees around the truck itself for a range of up to 15 metres. A radio location transmitter is fitted within the remote-control unit carried by the operator, so the truck knows exactly where they are at all times. Laser sensors track the operator as they walk around, as well as anyone else who is around the machine so there are no collisions or accidents. These collision sensors remain active even when the truck is put in manual mode so it will always react accordingly. There is also the option to have a 3D camera fitted which detects objects at a slightly higher level, like items sticking out of a rack. If it detects an obstacle, the truck can steer around it (if safe to do so), which is a feature unique to the STILL iGo neo. There’s a lot of technology that works behind the scenes to keep the operators safe and efficient without them needing to do anything.
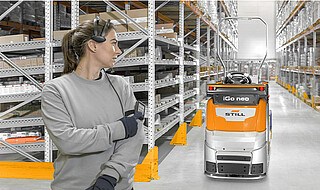
What are the benefits over a manual picker, both for operator and efficiency?
For the operator who already uses a manual picker, the autonomous order picker is a familiar product so it can be integrated into their job to make their lives easier. The operator and truck will work intuitively, so we estimate that performance can increase by up to 20%. Operator fatigue is reduced because they don’t have to spend time getting on and off the truck, plus the picker is programmed to stay at a pre-set distance from the racks for easy picking. The artificial intelligence capabilities of the machines enhance worker safety and our accident prevention ergonomics keep operators comfortable. You’ve also got increased reliability because you know potential damages are limited. Taking away some of the human element reduces the risk of collisions, particularly in situations where trucks run parallel to one another. You know that you’re not going to have a situation where one truck is accidentally driven into another.
What setup is required when using an autonomous order picker forthe first time?
The set-up for the iGo neo is minimal. You could essentially take it off the delivery truck, put in in the warehouse and set it to work. There is a small amount of operator setup to do in their day-to-day job, and more specific settings if you want it to work in a particular manner. At STILL we would allocate one point of contact for the customer, followed by a site survey to get an understanding of how the truck needs to operate and do some of the internal setup before it’s delivered. That way, we can drop the truck off and it’s ready to go. It’s not always required, but if we can understand the customer’s direct requirement then we can accommodate that way of working. For example, the operator may be picking from two sides rather than one or they may need to work slightly further away from the shelves (500 millimetres is standard). We can set all of that up for our customers. It’s worth mentioning however that anything related to safety like maximum speed or acceleration can’t be changed without confirmation from the safety representative at the customer’s site.
Does the operator need much training to start using an automated picker?
There will be an element of training to get the operator familiar with the vehicle. The operator may want to adjust the way they pick but as far as specific training goes, it’s just a case of understanding how the handset works and considering the safety features and how the vehicle reacts. It goes without saying but the operator wouldn’t need a special license to operate this type of truck.
Do you think semi-automated vehicles are here to stay or do you think full automation is on the horizon? If so, when do you think this is likely to happen?
I think this is one where anybody in this industry would need a crystal ball! I expect there will be a combination of semi-automated and autonomous vehicles in use for some time. In places like logistics distribution hubs or the food industry for instance, there’s still a need for that human intervention and I think that will continue for the foreseeable future. If you look at places where full automation is not implemented, it’s often because the cost of infrastructure deviations are too great. This is why semi-automation has proven so successful, because it doesn’t require a great deal of change.
Find out how our professional team can help
We can help your business improve warehouse efficiency, if you need advice on any of the topics or products mentioned above, please feel free to Contact us today!
Comments
No comments
Subscribe to the blog !
Be informed as soon as an article is published. You can unsubscribe anytime.
Leave a comment