Five ways warehouse automation can improve efficiency and wellbeing
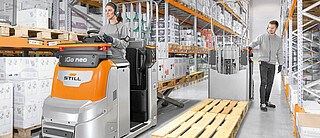
Automation is increasingly part of the conversation when it comes to discussions about the future of warehouse operations. Industry 4.0 was already driving more interest in automation, however the last 18 months has further accelerated growth in online shopping and this, combined with worker shortages impacting the supply chain is contributing to an increase in focus on automation to improve efficiency and wellbeing in the warehouse.
#1 Fill gaps in the workforce
Despite the boom in warehouse operations, finding qualified employees continues to be a challenge. In the MHI Annual Industry Report of 2019, 65% of businesses said that hiring qualified workers was extremely or very challenging.
Newly-emerging technology can help fill gaps in the workforce, whether it’s supporting operators with automated order pickers and semi-automated trucks, or taking over repetitive or dangerously strenuous tasks. While this increases operational efficiency because you don’t see the drop in productivity that would ultimately occur if a human was to perform a strenuous, repetitive task, but ultimately you’re creating a safer and more productive work environment.
#2 Minimise accidents
Accidents happen in almost every workplace and the nature of warehouse operations means the risk of injury to workers is fairly high. According to the British safety Council, around 1,300 UK employees are hospitalised each year following a forklift accidents alone.
Automation allows businesses to minimise the risk of accidents due to the safety features that come with Mobile Automation, hence preventing accidents from taking place. As an example, STILL’s range of semi-automated trucks come with cameras and sensors that stop them becoming too close to racks, workers or other vehicles, thus preventing collisions. If a tired operator fails to spot another vehicle rounding a corner, the safety system will automatically stop the truck before an accident can occur.
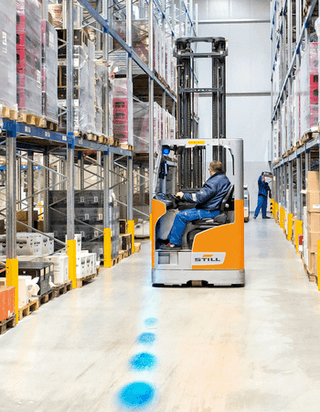
#3 Reduce mistakes caused by human error
Human error is somewhat inevitable but mistakes can prove costly to a warehouse. Whether it’s a truck that needs to be taken out of operation for repairs, damage to warehouse infrastructure or an incorrectly filled order which needs to be reprocessed; the result is delays and unexpected outgoings.
Take the online supermarket Ocado as an example. They process a huge amount, shipping over 330,000 orders per week, with complex orders that need to be accurate and perishable goods that need to be picked and shipped. Hundreds of human operators would need to work quickly, consistency and without error to fill that many orders. In cases like this, automation not only speed up the process; it reduces the margin for error caused by the intervention of an operator. This type of “goods to operator” system then passes the picked orders to staff who then pack and prep the order for delivery.
#4 Support workers in operations
Automation is not about eliminating warehouse jobs, it’s about improving them both in terms or worker wellbeing and operational efficiency. With the Guardian recently reporting that the UK is facing the worst labour shortages since 1997 and a shortage of workers currently disrupting the supply chain, supporting your workforce can help you retain qualified, experienced staff.
As well as eliminating the need for workers to perform strenuous or repetitive tasks which carry a high level of risk of accidents and repetitive strain injuries, automated systems can help support operators in their day-to-day tasks. Vehicles like STILL’s autonomous order pickers – the iGo neo – offer an extra level of support to workers and we estimate performance increase to be up to 20% with this product. For the operator who already uses a manual picker, the autonomous order picker is a familiar product so it can be integrated into their job and make their lives easier.
#5 Avoid worker fatigue
Worker fatigue can be an issue in any warehouse, but the challenges posed by e-commerce and the new world of 24/7 online ordering have compounded this issue as workers are required to work harder and faster to meet the increasing demands of customers. With today’s warehouses taking up more than 30% more space than they did a decade ago, people are also required to travel greater distances during the course of their shift. While it is somewhat inevitable that humans will tire during a long shift and automation helps take some of the strain. Even fairly low levels of automation like driver assistance systems can support truck drivers by assuming individual tasks and freeing the operator to focus on bigger tasks.
With an efficient and happy workforce being supported by automated systems, warehouses can thrive in today’s demanding environment and ensure they are prepared for the challenges of the future. Utilising automated process and machinery brings together the benefits of technological performance and human understanding.
Comments
No comments
Subscribe to our blog!
As soon as a new article is published, we will notify you! You can unsubscribe at anytime.
Leave a comment