How our Industry 4.0 innovations are driving supply chain efficiency
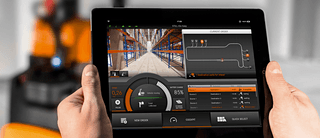
The technology boom of recent years has had a big an impact on warehousing, logistics and the supply chain as a whole. The interconnectivity between physical goods/process and digital, data-driven systems has become known as Industry 4.0 and it has revolutionised the supply chain.
The increase in access to real-time data from one end of the supply chain to the other has allowed logistics companies to transform how they operate, increasing productivity and reducing risk through efficient asset utilisation, automated processes and driving labour efficiencies through safety enhancements and operator support.
In this article, we look at some of the developments that Industry 4.0 is bringing to the logistics industry and how they are driving supply chain efficiency.
Data analysis for fleet management
New technologies have given access to unprecedented levels of data that managers have, in the past, only been able to dream of. The marriage of digital and physical systems has allowed logistics operators to see exactly how their vehicle fleet is operating and plan ahead using fleet management software. This 24/7 data allows managers to identify inefficiencies in the fleet and ensure that trucks are operating at maximum performance levels, something that is becoming more important as 24 hour operations become increasingly common.
The fundamental goal of the software is to allow businesses to attain cost savings and manage their fleet operations more efficiently. It focuses on the utilisation of vehicles and identifying patterns and areas for improvement. Fleet management software can take a huge amount of data about an entire fleet and displays it in one place so it can be easily reviewed and acted upon to drive down costs and increase efficiency in warehouses and distribution centres.
Safety enhancements for operators
As human operators are put under increasing pressure to meet the demands of the supply chain and automation is increasingly being used to support and enhance distribution centre processing, the importance of safety in logistics cannot be overlooked. A more demanding supply chain results in a busier distribution centre and, where you have more people, goods and vehicles interacting, the risk of accidents increases. As well avoiding potentially costly damage to stock and infrastructure, the safety features now available on machinery and trucks can help ensure worker safety and enhance wellbeing. Warehouse vehicles like semi-automated trucks can be programmed to recognise impending collisions – whether that’s with other vehicles, pedestrians or warehouse infrastructure – and take action to avoid it.
Human error can be costly to a business, whether it’s simply a reduction in productivity as the shift wears on or mistakes such as damaged products, incorrect orders or slow processing, and the developments of Industry 4.0 can help staff meet the demands placed upon them in a safe and efficient way.
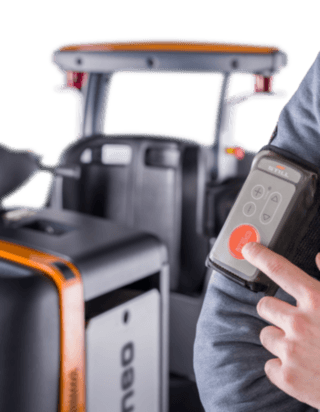
Semi-autonomous trucks and automated processes
Semi-autonomous machines and automated process have become an essential component in increasing efficiencies at many stages of the supply chain. In warehouses for example, the average site size has increased 30% compared to a decade ago with workers being required to travel greater distances over the course of their shift. Automation isn’t necessarily about replacing human operators as is often thought, it’s about supporting them and allowing them to do their jobs more quickly and easily.
With the safety features and data analysis advances outlined above, the automisation and semi-automation of warehouse vehicles and processing systems have seen some of the biggest updates in the revolution of Industry 4.0. Sophisticated sensors and programming allow vehicles to follow pre-set pathways and adhere to on-site guidelines around speed and manoeuvrability, allowing them to be deployed where needed to support the supply chain. Historically, many automated systems and robotic operating systems were kept separate from human operators for health and safety reasons which could limit efficiencies gained by automation but the enhanced safety features coming into play in recent years is allowing for more integration.
Smart stock management based on data modelling
Having immediate access to data from different sources allows businesses to plan ahead when it comes to resources and stock management. Without relevant information like projected peaks in demand, current stock levels, storage capacity, upcoming orders, warehouses and distribution centres were forced to keep high levels of stock or risk running out of key components and goods. With data-modelled stock management, this is no longer the case. And this development isn’t limited to single warehouses. Companies with interconnected operational data systems can have visibility of the entire supply chain from top to bottom and identify potential issues with inventory levels and order processing before they become costly errors.
The impact of Industry 4.0 on supply chain logistics has been huge and new technologies and innovations continue to offer new opportunities for warehouses to work smarter. Improving efficiencies isn’t just important, it’s rapidly becoming critical at a time when national and international supply chains are facing more demands than ever before. However, with every challenge comes opportunity, and the technological advances brought forward by Industry 4.0 gives businesses the chance to thrive.
Comments
No comments
Subscribe to our blog!
As soon as a new article is published, we will notify you! You can unsubscribe at anytime.
Leave a comment