How automotive logistics is being driven forward by STILL
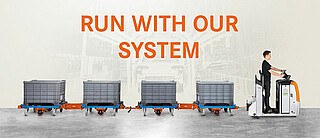
Every second counts in automotive logistics and choosing the right materials handling equipment to work with your assembly lines can save time and money. But with ever-changing vehicle customisation now available to the consumer, how do manufacturers keep their costs down? In this interview, we ask Andrew Dean, National Key Accounts Manager and automotive logistics expert how STILL is solving new challenges for its customers.
What role does materials handling equipment play in the automotive industry?
The role of materials handling in the automotive industry is huge, and without it the way cars are manufactured and customised today just wouldn’t be possible. As consumers, we expect to be able to visit a website or a showroom and configure a car to our individual specification. This will include much more than paint colour, wheels, seat trims, steering wheels and entertainment systems – there are so many options which can be chosen by the customer. And the demand to have value-for-money customisation delivered quickly is ever-increasing.
To achieve this level of tailoring whilst offering a fast lead time, premium car manufacturers like BMW looked at developing materials handling equipment designed specifically to work with the manufacturing process of their cars. In partnership with them, STILL developed the Tugger Train, a type of truck which could deliver parts and components at exactly the right point in the assembly line.
What challenges in automotive manufacturing has STILL helped overcome?
Vehicle customisation is a major challenge within automotive manufacturing, as I explained above consumers are wanting more customisation and individuality in a car. This creates a much more complex supply chain of different parts and components produced by suppliers. The manufacturers we work with are looking to make that supply chain as efficient as possible by minimising the components made and stored on site at the factory and supplying them into the assembly line at the right time. One way we are improving efficiency is by working with vehicle manufacturers tier 1 suppliers to introduce Tugger Trains and more efficient logistics processes. If you take for example a car seat supplier; following our support, each component and customisable element of the seat is delivered to the assembly line as efficiently as possible. For the vehicle manufacturer having each of their major suppliers operating efficiently brings a cost and time saving benefit, which they can then pass on to the customer.
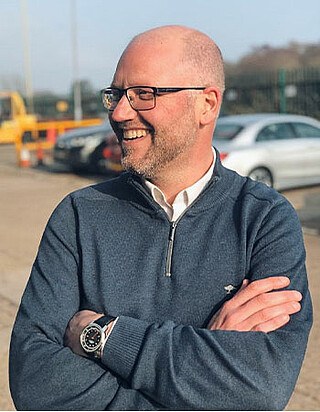
What efficiencies can Tugger Trains bring to vehicle manufacturing?
The Tugger Train was developed by automotive engineers and my colleagues in Germany; they observed the challenges manufacturers were facing when integrating vehicle customisation into ‘Just In Time’ (JIT) and ‘Just in Sequence’ (JIS) manufacturing processes.
What the automotive industry were looking for was a vehicle system that was low cost and simple, but also offered flexibility to handle the increasing range of different components ordered from the customer. The concept of a truck pulling a train of parts is nothing new, but when STILL developed the Tugger Train, our aim was low cost flexibility. As a result, we have a truck that is 80% standard and 20% customisable. That 20% is where it really counts, here we work with the manufacturer to develop frames and parts carriers that are tailor-made to a specific assembly line. The Tugger Train then becomes an integral part of the assembly line, bringing time saving efficiencies, improving health and safety for the workforce and saving on costs.
One example of this integration is a recent year-long project with the well-known, largest UK car manufacturer where STILL developed a solution that can handle around 80 different load sizes, all based on our standard Tugger Train. This flexibility is a real winner for us, and what makes STILL a strong player in the automotive industry.
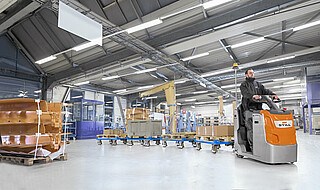
How is STILL helping improve processes like ‘Just-In-Time’ in the context of automotive manufacturing?
Understandably every second counts with ‘Just-in-Time’ and ‘Just-in-Sequence’ manufacturing processes. To help ensure our equipment like the Tugger Train is really working with that process, we support our customers over long test cycles to refine how efficiently our equipment is delivering parts to the assembly line.
This can involve part storage and re-supply using the Tugger Train, how long it takes for the technician to access the part, and for the train to be re-stocked for example. Ergonomics play a big part in improving the process, the parts delivery needs to work alongside for a technician that could be 5ft or 6.5ft tall. So, in the pilot phase of developing an assembly supply system, we’ll adjust the heights and angles of the parts carriers on the Tugger Train, creating a tailor-made solution for the technicians working on the assembly line.
Some of the Tugger Train systems we developed also have rotating carriers, so if you’re working on the assembly line and the parts you need have run out on your side of the carrier, but there’s buffer stock on the other side, pressing a button rotates the carrier around allowing you to access a fresh parts supply, while the other side is re-supplied. The advantage of this system is zero waiting time for the carriers to be replenished with new parts, all achieved through a standard Tugger Train with a carrier system, customised to the specific process of that assembly line.
Will digitisation change the automotive supply chain process?
I wouldn’t say digitalisation will change things, I believe it already has made some significant changes and improvements. Firstly, STILL FleetManager™ software has made factories safer places, ensuring only people with the correct permissions or licence can drive the equipment. Plus, it operates as a black box in the event of an accident, data such as speed and location are all recorded. Allowing fleet managers to identify how the accident happened and what can be done to prevent it in future. Taking data sharing further we will regularly work with customers on identifying trends in their fleet, to help them improve efficiency and get value for money out of their equipment. We can help spot inefficiencies like if a piece of equipment isn’t being used enough or if the truck is doing a lot of horizontal movement but not much vertical lifting then we would analyse whether the carriers are configured correctly to suit the technicians on the assembly line.
STILL is making all of this data more accessible too, moving away from software and bringing it together into an online portal with other tools like STILL neXXt fleet, which gives a complete view of equipment performance and service maintenance. This tool is helping answer a lot of customer requests when it comes to measuring maintenance and managing costs of their fleet, it’s a regular part of the conversations we’re now having with our customers.
Find out how our professional team can help
With industry experts in every region, STILL offer an efficient and market leading support offering to warehouse managers. Speak to our experts to discover how we can improve the efficiency of your fleet and MHE. Contact us today!
Comments
No comments
Subscribe to the blog !
Be informed as soon as an article is published. You can unsubscribe anytime.
Leave a comment